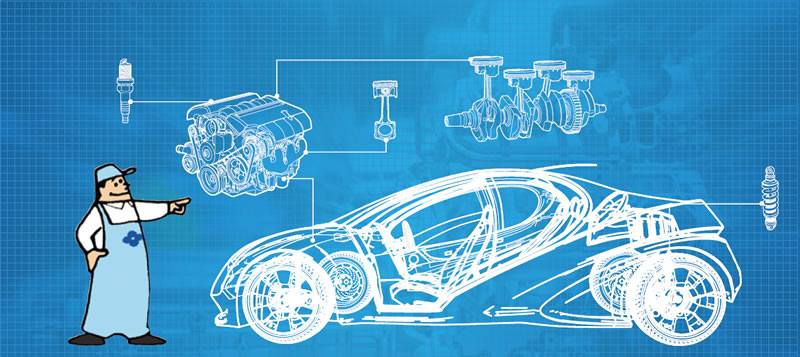
เครื่องยนต์ได้ถูกผลิตขึ้นในประเทศอย่างสมบูรณ์ ทั้งแบบเครื่องยนต์ดีเซลและเครื่องยนต์แก๊สโซลีน ในเครื่องยนต์ซึ่งถือเป็นหัวใจของรถยนต์ประกอบไปด้วยชิ้นส่วนต่างๆ มากมายหลายรายการ ในการผลิตชิ้นส่วนดังกล่าวโดยเฉพาะชิ้นส่วนหลักสำคัญๆ จะต้องใช้เครื่องมือตัดพิเศษที่ออกแบบเฉพาะ โดยมีโจทย์ที่ท้าทายเป็นอย่างมากทั้งความละเอียด เที่ยงตรง ไปจนถึงความคุ้มค่าหรือต้นทุนการผลิต ในบทความฉบับนี้ทางบริษัท ซูมิโตโม อีเล็คตริก ฮาร์ดเมทัล แมนูแฟคเจอริ่ง (ประเทศไทย) จำกัด ขอกล่าวถึง การออกแบบเครื่องมือตัดขึ้นรูปโลหะชิ้นส่วนประกอบหลักที่สำคัญของเครื่องยนต์ คือ เพลาข้อเหวี่ยง (Crank shaft) ก้านสูบ (Connecting Rod) เสื้อสูบ (Cylinder block) ฝาสูบ (Cylinder head) และเพลาลูกเบี้ยว (Cam shaft) ซึ่งชิ้นส่วนดังกล่าวเป็นส่วนสำคัญในการขับเคลื่อนของเครื่องยนต์ ดังนั้นในกระบวนการตัดแต่งขึ้นรูปโลหะต้องให้ความพิถีพิถันในการเลือกและควบคุมจุดที่สำคัญในการทำงานเป็นอย่างยิ่ง
ชิ้นส่วนหลักส่วนแรกคือ เพลาข้อเหวี่ยง (Crank shaft)
มีหน้าที่ในการหมุนเพื่อบังคับก้านสูบให้เคลื่อนที่และควบคุมจังหวะอัดน้ำมันในกระบอกสูบซึ่งกระบวนการตัดแต่งขึ้นรูปโลหะที่สำคัญคือ การกัดเพลาเยื้องศูนย์กลาง (Pin Milling) โดยทั่วไปจะใช้เครื่องจักรที่ออกแบบมาเป็นพิเศษเพื่อรองรับการหมุนแกว่งหนีศูนย์กลาง และใช้เครื่องมือตัดแต่งขึ้นรูปโลหะที่เรียกว่าพินมิลลิ่งคัตเตอร์ (Pin milling cutter) ซึ่งในกระบวนการกัดนี้ เป็นการกัดหยาบและมีแรงกัดที่สูงมาก ดังนั้นจุดที่สำคัญที่ต้องพิจารณาคือการออกแบบคัตเตอร์ที่ต้องจับยึดให้เข้ากับตัวอะแดปเตอร์ Adaptor) ในเครื่องจักรให้แน่นและมีความแข็งแรงที่มาก (High Rigidity) ซึ่งส่วนใหญ่จะเลือกใช้วิธีการจับยึดแบบ เทเปอร์ (Taper clamp) ที่ให้ความแข็งแกร่ง และยึดแน่นที่สุดอีกส่วนที่สำคัญคือการยึดเม็ดมีดควรเลือกแบบยึดตามแนวนอนเพื่อเพิ่มความแข็งแกร่งในการรองรับการกระแทก รวมถึงควรเลือกการออกแบบเม็ดมีดที่มีมุมคายที่มากเพื่อลดแรงในการกัด ประกอบกับการเลือกเกรดเม็ดมีด ควรเลือกให้สามารถทนทานต่อการแตกร้าวเนื่องจากอุณหภูมิและการกระแทก (Thermal Cracking) การเจาะรูน้ำมัน (Oil hole drilling) ในกระบวนการนี้จะเป็นการเจาะรูขนาดเส้นผ่านศูนย์กลางที่เล็กและลึกมาก (15-25 เท่าของขนาดเส้นผ่านศูนย์กลาง) ประกอบกับเป็นการเจาะลงในผิวโค้งของแกนเพลา โดยปัญหาที่พบบ่อยคือการหักของดอกสว่าน ดังนั้นในการออกแบบกระบวนการควรเริ่มต้นจากกระบวนการกัดด้วยเอ็นมิลด์ เพื่อปรับให้ผิวโค้งเป็นผิวเรียบก่อน จากนั้นเลือกใช้ดอกสว่านเจาะนำที่มีมุมองศาดอกสว่านมากกว่าดอกสว่านเจาะตามประมาณ 10 องศา ส่วนสุดท้ายจะเลือกใช้ดอกสว่านเจาะลูกลึกที่มีความสามารถในการหักเศษและระบายเศษออกจากรูได้อย่างมีประสิทธิภาพ การกลึงงานปาดหน้าเพลาข้อเหวี่ยง ( Flange face Turning) ปัญหาที่พบส่วนใหญ่คือการแตกบิ่นที่ปลายคมตัดเนื่องจากเป็นกระบวนการกลึงแบบกระแทก (Interrupted cutting) ดังนั้นควรเลือกเกรดเม็ดมีดที่มีความทนทานต่อการแตกบิ่นและมีความเหนียวพิเศษ
ชิ้นงานตัวต่อมาคือ ก้านสูบ (Connecting rod) เป็นชิ้นส่วนที่จับยึดเข้ากับเพลาข้อเหวี่ยงและลูกสูบ ดังนั้นความสำคัญคือการสวมประกอบ โดยมีกระบวนการตัดแต่งขึ้นรูปโลหะที่สำคัญคือการคว้านรู (Boring) ปัญหาที่พบส่วนใหญ่คือขนาดของเส้นผ่านศูนย์กลางมีค่าความคลาดเคลื่อนที่ไม่เสถียร ดังนั้นควรพิจารณาเลือกใช้เม็ดมีดที่ผลิตโดยการเจียร์ (G-Class insert) ในกระบวนการคว้านละเอียด เพื่อให้ได้ขนาดเส้นผ่านศูนย์กลางที่คงที่มากขึ้น
การเจาะรูทะลุที่มีทางออกเป็นผิวเอียง ปัญหาที่พบคือการเอียงหนีศูนย์กลางของรูชิ้นงาน (Concentric problems) ดังนั้นการเลือกดอกสว่านควรเลือกดอกสว่านที่สามารถประคองแรงจากแนวข้างได้คือดอกสว่านแบบดับเบิ้ลมาร์จิ้น (Double margin drill)
ชิ้นงานตัวที่ 3 คือ เสื้อสูบ (Cylinder Block) เป็นชิ้นส่วนที่มีการสวมอัดด้วยกระบอกสูบ และนำไปประกอบเข้ากับฝาสูบอีกครั้ง กระบวนการที่สำคัญคือ การปาดหน้าชิ้นงาน (Surface Milling) ปัญหาที่พบส่วนใหญ่คือความเรียบผิว (Surface Roughness) และการสะท้านเนื่องจากแรงกัด (Chattering) ดังนั้นการเลือกคัตเตอร์ควรเลือกคัตเตอร์ที่สามารถปรับตั้งความสูงต่ำของเม็ดมีดได้ (Height Run-out adjustable) โดยในการปรับควรมีค่าความต่างของความสูงโดยรอบตัวไม่เกิน 0.01 มิลลิเมตร เพื่อการควบคุมผิว และเลือกคัตเตอร์ที่ใช้แรงตัดที่น้อย โดยพิจารณาจากค่ามุมคายตามแนวแกน (Axial Rake angle) เพื่อลดแรงสะท้าน
การเจาะรูฝั่งหัวสกรู (Bolt Hole drilling) จะเป็นการเจาะรูที่มีขนาดเส้นผ่านศูนย์การหลายขนาดและปัญหาที่พบส่วนใหญ่คือเวลาในการผลิตและจำนวนดอกสว่านที่ใช้มากเกินไป ดังนั้นควรพิจารณาลดจำนวนดอกสว่านโดยการเลือกใช้ ดอกสว่านประเภท Step drill หรือ Subland drill ซึ่งดอกสว่านทั้งสองประเภทนี้เป็นการรวมกันดอกสว่านหลายๆ เส้นผ่านศูนย์กลางเข้าในตัวเดียวกันเพื่อลดเวลาในการผลิตและเพิ่มความแม่นยำของรูได้อีกด้วย
ชิ้นงานตัวที่ 4 คือ ฝาสูบ (Cylinder Head) ส่วนใหญ่ใช้วัสดุประเภทอะลูมิเนียมเป็นชิ้นส่วนที่ประกอบจากเสื้อสูบและภายจะประกอบด้วยวาล์อัดฉีดน้ำมัน ซึ่งมีความสำคัญในการควบคุมขนาดของบ่าวาวล์ในงานแมชชีนนิ่ง (Valve seat machining) การกัดบ่าวาวล์ (Valve seat machining) จะเป็นการกัดงานที่ต้องการความเรียบผิวและมีความแม่นยำสูงเพื่อป้องกันการรั่วไหลของน้ำมันเวลาทำงานปัญหาส่วนใหญ่ที่พบคือผิวชิ้นงานเป็นฝ้าขาวเนื่องจากการพอกของอะลูมิเนียม (Built up Edge) ในกระบวนการกัดละเอียด ดังนั้นควรพิจารณาการเลือกคัตเตอร์ที่มีคมตัดที่แหลมคมและใช้วัสดุประเภทเพชรสังเคราะห์ หรือ PCD (Poly Crystalize Diamond) มาเพื่อป้องกันปัญหาดังกล่าว
ชิ้นงานตัวสุดท้าย คือ เพลาลูกเบี้ยว (Cam shaft) เป็นชิ้นส่วนที่มีหน้าที่ในการหมุนปรับจังหวะในการทำงานของลูกสูบให้เดินอย่างราบรื่น โดยส่วนใหญ่จะใช้กระบวนการกลึงเก็บละเอียดเพื่อให้ได้ชิ้นงานที่มีความแม่นยำสูงการกลึงเพลาลูกเบี้ยว ส่วนใหญ่จะใช้เม็ดมีดมุม 35 , 55 และ 60 ในการกลึงเก็บละเอียด ซึ่งเป็นมุมที่มีขนาดเล็กถึงปานกลาง ประกอบกับชิ้นงานก่อนการกลึงมีลักษณะผิวไม่เรียบและเป็นการกลึงเข้ามุมซึ่งปัญหาที่พบส่วนใหญ่คือเม็ดมีดมีการแตกบิ่นได้ง่าย ดังนั้นสิ่งควรพิจารณาเป็นอย่างยิ่งคือการเลือกเกรดเม็ดมีดที่มีความเหนียวพิเศษ Higher toughness) และควรเลือกด้ามมีดที่มีความแข็งในการจับยึดเพิ่มเติมอีกด้วย